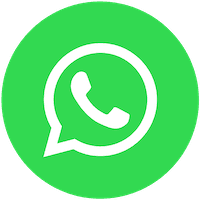
Marine Fender Replacement Services | Offshore & Port Solutions
Jul 9, 2025
Marine Fender Replacement at Jebel Ali Port | Rope Access Execution for Dubai Petroleum
Marine fender replacement using rope access was successfully executed by AIMMS Group for Dubai Petroleum at LNG Jetty Terminal 4, Jebel Ali Port. This critical project involved replacing large fenders over days schedule and highlighted our specialized capabilities in rope access and marine infrastructure maintenance. The operation was completed with a strong focus on safety, precision, and minimal disruption to ongoing port activities.
Project Overview
Client: Dubai Petroleum
Location: LNG Jetty Terminal 4, Jebel Ali Port (JAFZA)
Support Vessel: DSV MAHARA
Scope: Replacement of marine fenders
Team: 6 rope access technicians + 1 IRATA Level 3 Supervisor
Support Equipment: Crane-assisted lifting, chain blocks, and vessel-based hoists
Why Marine Fender Replacement Matters
Marine fenders are vital for absorbing the kinetic energy of docking vessels and safeguarding both the port infrastructure and vessels. Over time, continuous impact, corrosion, and weather exposure degrade their performance. Dubai Petroleum identified the urgent need to replace fenders to ensure continued safe berthing for offshore support vessels.
If you're interested in more marine-related services, visit our blog on marine inspection and survey services in the UAE and India.
Our Rope Access Strategy: Safe, Fast, Cost-Efficient
AIMMS Group opted for rope access methodology over conventional scaffolding or barge-based solutions to address the limited access space, tidal changes, and vessel traffic. This minimized operational disruption while ensuring crew safety and efficient execution for disruption.
Learn more about our structural maintenance via rope access.
Project Execution progress
Task 1 : Removal of Old Fenders
Rope access technicians conducted safety briefings and installed rigging systems as per IRATA and HSE protocols.
Using chain blocks and auxiliary hoists, the team began the careful dismantling of shackles and supporting components.
Old fenders were unbolted, inspected, and safely lifted off using crane and vessel coordination.
Task 2 : Installation of New Fenders
The new fenders were aligned and lowered into position using taglines, webbing slings, and precise crane maneuvering.
Technicians secured upper and lower chain attachments, pad-eyes, and shackle points.
After double-checking all bolted connections, the rigging was removed, and daily HSE documentation was submitted.
Key Safety and Technical Measures
All personnel were IRATA certified and trained professionals.
Tools and equipment followed ISO and IRATA standards, with double fall arrest systems, tool lanyards, and rope protectors.
A fall proof rescue plan and exclusion zones were implemented.
Daily toolbox talks, buddy checks, and PPE compliance were enforced throughout the operation.
Explore how we apply this rope access approach to blasting and coating work as well.
Highlights from the Project
According to the approved method statement:
Anchor points with a minimum load capacity of 15kN were used.
Mechanical Advantage 6:1 hoist systems supported material movement and rescue readiness.
Team were mobilized in short term notice.
Executed the work with 100% safety.
Overcoming Challenges at Jebel Ali Port
Executing a marine fender replacement at a live port facility like LNG Jetty Terminal 4 presented multiple operational and environmental challenges — each of which required tailored solutions to maintain safety, schedule, and quality.
Limited Access & Tidal Conditions
The work zone was directly along the quay wall, with restricted horizontal access and no scaffolding options. Changing tides added complexity, as access height and safe working zones varied throughout the day. Rope access provided the agility and flexibility needed to work across shifting tidal levels.
Corroded Fittings and Hardware
Some of the existing shackles, pad-eyes, and fender chains were heavily corroded, requiring extra effort to clean, loosen, and safely dismantle them. Our technicians used rust remover, manual tools, and mechanical hoists to disassemble the rusted components while suspended on ropes.
Complex Lifting and Alignment
The replacement fenders were large, heavy units, requiring crane-assisted lifting in confined berthing spaces. Ensuring accurate alignment of the new fenders while suspended — and tightening bolts to manufacturer torque specifications — demanded both skill and coordination between the crane operator and rope access team.
Strict Safety Compliance in a High-Risk Zone
Working over water, at height, and with heavy loads meant every movement had to be meticulously planned and risk-assessed. Exclusion zones, double fall arrest systems, edge protection, and a rig-for-rescue plan were all mandatory and actively monitored by the IRATA Level 3 Supervisor.
Why Dubai Petroleum Trusts AIMMS Group
At AIMMS Group, we are known for:
Decades of marine and offshore maintenance experience
Efficient coordination with crane, vessel, and port authorities
Proven track record in fender replacement, jetty repair, corrosion protection, and rope access inspections & Maintenance.
Experienced rope access technicians.
Need Marine Fender Replacement in the UAE?
Whether at ports, jetties, offshore platforms, or marine terminals, AIMMS Group is your trusted partner for specialized access solutions, marine maintenance, and IRATA-certified services.

AIMMS Group is a UAE based Marine inspection, maintenance and rope access services provider having delivery centers in India, KSA & UK. Our NDT & UT Gauging team is well versed with oil, gas & marine industries and have delivered services to leading organizations in the sector across the waters. Our rope access based mechanical team is well equipped & skilled to meet corrosion protection, welding , fabrication, painting requirements of any industries.
FOLLOW US
Connect for real-time updates and expert perspectives on industry trends.
HEADQUARTERS
M-35- 16th St, Building 3,
Musaffah,B-2- 18, ICAD, Abu Dhabi, UAE.
PHONE
SERVICES
Copyright © 2024 AIMMS Group. All Rights Reserved.